InFlex™ Flow Control Valve (FCV™)
U.S. Patents 5,316,081 and 6,273,195
Baski, Inc. made the world's first downhole flow control valve in 1992, which was installed in Highlands Ranch, CO for Centennial Water and Sanitation District. Since then, Baski has manufactured over 250 FCVs, which have been installed mostly in the western US.
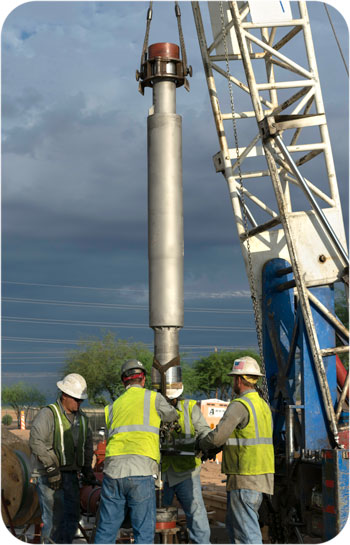
For overview product and application information, click here to download our most recent Catalog 6 (PDF). Its pages 22-25 provide an introduction to our FCV™, technical drawings, and specification worksheets.
For us to determine which FCV™ will be best for your application, please download the FCV worksheet. Fill it out with as much information as you have available, and email it to us.
The InFlex™ Flow Control Valve (FCV™) is a fluid-actuated valve that permits pumping water to the surface or regulating the flow of water from the surface into the well, while using the same column pipe and maintaining a column of water in it at all times. The InFlex™ FCV™ may be used in conjunction with a submersible pump or a vertical turbine pump for Aquifer Storage and Recovery (ASR) and Aquifer Thermal Energy Storage (ATES) applications. Advantages of the InFlex™ FCV™ include:
Impressive Performance
Testing at the factory and field use of the InFlex™ FCV™ confirm that it effectively adjusts and holds desired injection rates. Because of its unique design features, including no sliding seals to fail, it is the most durable and versatile valve on the market.
Cavitation-Free Design
The key to the successful control of the injection water through this valve is its long, adjustable, annular-gap flow path through a series of circular annular orifices. This flow path provides non-cavitating head loss that is easily controlled by changing the gap between the annular orifices and the rubber element. Stainless steel channels are a part of the adjustable flow system and stabilize the rubber element as it is pushed down and stretched by the inflation liquid.
Impossible to Sand-lock
By design, there is no place for sand to collect; therefore, the InFlex™ FCV™ cannot sand lock. It is impossible for the rubber element to "stick" at any time during pumping or injection, as there are no sliding surfaces to become "stuck" due to sand-locking.
Wear-resistant
The InFlex™ FCV™ is extremely wear-resistant due to its rubber control element, similar to slurry pumps which are rubber lined to reduce wear. Due to its low-velocity, cavitation-free flow, the InFlex™ FCV™ resists sand and silt far better than conventional valve designs. Conventional valves have all of their pressure loss (at high velocities) across only one orifice stage, leading to wear from suspended solids and erosion with cavitation.
Ask about our 5-year limited warranty
The InFlex™ FCV™ utilizes a reinforced rubber element, the only “moving” part. This element is an adaptation of the element that has been successfully used in our inflatable downhole packers in demanding open-hole conditions for over three decades. All metal parts of the valve are constructed of stainless steel. Other more corrosion-resistant alloys are optional for aggressive environments.
Wide Range of Injection Capacities
Our InFlex™ FCV™ offers injection capacities of 10,000 gpm and higher with driving heads of 20 to 3,000 feet. All of the valves are infinitely adjustable from drip-tight shut-off to maximum flow. Furthermore, their maximum flow rate can be limited by using two control lines.
Use free Adobe Reader® to view and print the PDF documents available on this website. 